JLG scissor lifts provide greater uptime and reduce the need for recharging when compared to other models. By incorporating the latest advances in technology, JLG is able to offer innovative features that increase productivity and safety on the job site. With fewer scheduled services required, a quieter work area, no dependency on hydraulic oils and zero emissions, our electric scissor lifts are designed for maximum efficiency. Opting for an electric man lift from JLG can be beneficial in terms of both cost savings and improved performance.
Unfortunately, in some cases, JGL scissor lifts can give a warning code or a flashing warning light during operation. In this article, we will explain what the error codes of your JLG scissor lift mean and what to do if the JLG Scissor Lift Warning Light is Flashing.
See also: Jlg Boom Lift Warning Lights
JLG Scissor Lifts Fault Codes
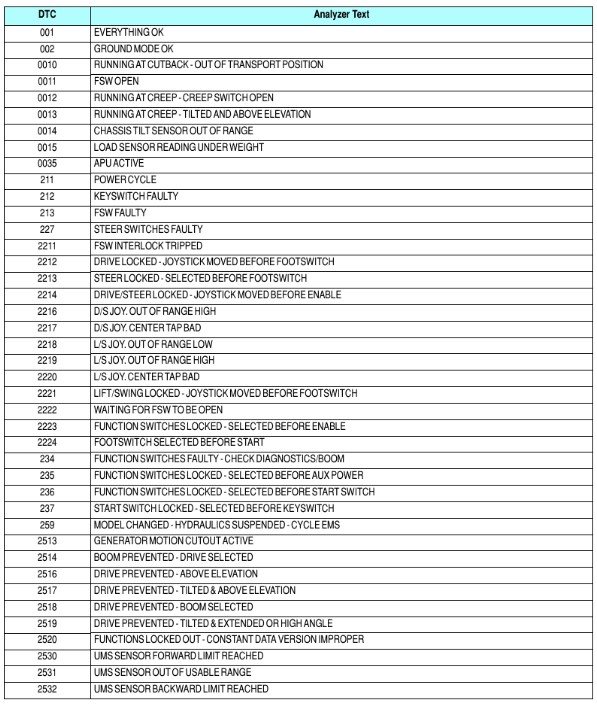
If you see a flashing JLG Scissor Lift Warning Light on your forklift, don’t worry! Sometimes this can be a simple warning light and does not mean that there is anything wrong with your lift. Warning lights that come with some error codes can be a serious fault.
If you see an error code that prevents the lift from working, you can check the codes in the list below. By knowing what the error codes mean, you can solve problems with your JGL Scissor Lift.
212 – Faulty Keyswitch
This fault message states that both platform and ground modes are selected simultaneously. In order to check this, it is necessary to first check the key switch function as well as all of its wiring. If either of these factors have not been correctly configured or installed, then the fault will persist until the issue is resolved.
221 – Horn Permanently Selected
This fault message is related to the horn switch on the platform being closed during power-up. If this occurs, it can cause damage and should be checked for any obstructions or other issues that may have been caused. The user should check if the horn is damaged, obstructed or jammed in order to prevent further damage from occurring. It is important to keep an eye out for this fault message as it could indicate a serious underlying issue with the platform’s components.
226 – Accelerator Faulty
This fault message is indicating that the accelerator joystick signal is outside of the acceptable range of 0.5V – 4.5V. In order to troubleshoot this issue, it is advised to check and see if centering the joystick will clear any diagnostic trouble codes (DTCs) by performing a power cycle on the system. If this does not resolve the issue, then further investigation may be required in order to properly diagnose and fix any underlying issues with the accelerator joystick or its corresponding components.
231 – Function Problem – Lift Permanently Selected
Ground control personnel experienced a fault message regarding the lift switch during power up in ground mode. The “Function Problem – Lift Permanently Selected” description indicated that the lift switch had been inadvertently closed either up or down while powering up. It is important to ensure that all switches are open prior to powering on any system, as closing them can result in undesired consequences related to their function.
233 – Function Problem – Brake Release Permanently Selected
This fault message indicates that the manual brake release switch was closed during power-up. To rectify this issue, it is necessary to check if the brake release switch is obstructed or jammed. If the switch is found to be blocked or stuck in a position, it should be cleared and operated correctly according to manufacturer’s instructions. In addition, all related connections should be inspected for any signs of defect before attempting further troubleshooting.
251 – Elev Angle Sensor Faulty
The Fault Message for the Elevation Angle Sensor is indicating that the input voltage is outside of its acceptable range. In order to troubleshoot this issue, it is important to verify that the platform elevation sensor is securely mounted and undamaged, as well as check the wiring connected to it. If any irregularities are found during this inspection, corrective action should be taken immediately in order to prevent further damage or malfunctions from occurring.
314 – Auxiliary Circuit – Open Relay
The auxiliary relay failed to close when power was applied. To investigate, it is necessary to inspect the coil of the auxiliary relay and related wiring for any issues or other causes. If anything appears out of order, corrective action should be taken according to the applicable service documentation.
441 – Battery Voltage Too Low
The power module detected a battery voltage under 14.5V, resulting in a fault message of “Battery Voltage Too Low”. It is advised to recharge the batteries or check for any damaged ones as part of an inspection process. If these actions are taken and the problem persists then further measures may need to be implemented.
775 – Open Circuit Field Wiring
The “Fault Message: Open Circuit Field Wiring” indicates that the system module applied field current to the drive, steer, and lift functions but was unable to regulate the desired current. This situation is likely caused by improper field wiring or a damaged motor in the system. To properly diagnose this issue it is necessary to check for any open circuit connections and assess whether there are any signs of damage on the motor itself.
In Conclusions, if you’re experiencing a JLG Scissor Lift Warning Light Flashing on your truck, don’t worry! This is just a warning light and doesn’t mean that there’s anything wrong with your lift. In fact, it could simply mean that the lift has been turned off accidentally or that there’s something blocking the power to the lift. If you think there might be something preventing the lift from working, please contact JLG customer service for assistance.
I have encountered this issue myself when using JLG scissor lifts. I had to check all the wiring and connections to make sure that the lift was getting the proper power. This is not always the case, though. In some instances, the warning light can be caused by a malfunctioning part or a lack of maintenance. In any case, it is important to seek professional help when dealing with JLG scissor lifts so that the issue can be resolved quickly and safely. Has anyone else encountered this issue and found a solution? How did you go about resolving it?