John Deere 3025d has been the go-to mower for many landscapers who dream of an even lawn. However, there have been some trivial issues that have caused concern for beginners to this model of mower. Issues such as loose blades, transmission failure and overheating engines can hinder its performance and cause frustration.
Fortunately, this article provides a comprehensive guide on how to deal with these issues and allow users to get back to their lawns quickly. It is well researched and offers a wide range of information that covers all queries related to John Deere 3025d. This makes it the perfect reference point for any beginner or experienced user looking for help in tackling problems they may experience while using the machine.
General article: John Deere Tractor Warning Lights Meaning
5 Common John Deere 3025d Problems (Solution List)
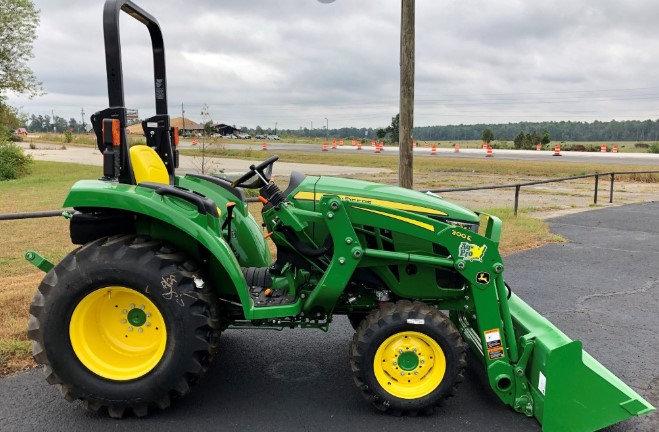
Let’s examine John Deere 3025d Problems together. Divided into five main headings, we have compiled the problems and solutions that may be within these problems for you.
1.Diesel Engine Troubleshooting
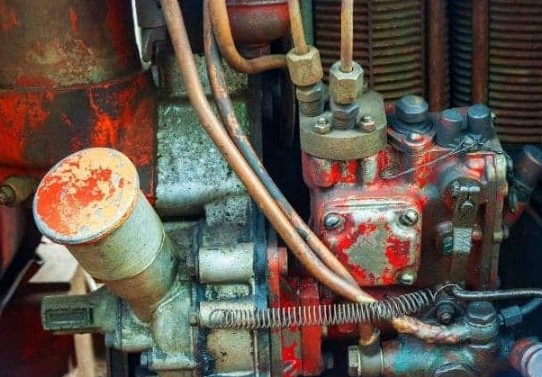
- Engine starts up hard or doesn’t start: The fuel filter element is a critical component that needs to be maintained in order for the vehicle to run properly. If it is determined that the filter element is dirty, it must either be cleaned or replaced with a new one. Additionally, air trapped in the fuel system should also be bled. Lastly, fuel injection nozzles may need to be inspected and potentially replaced if they are faulty or clogged. If there appears to be an issue with the fuel injection pump itself, repair or installation of a new pump might prove necessary.
- Engine stalls during operation: A common issue that can arise during operation is engine stalling. This is often caused by a fuel injection pump timing being wrong, and the remedy for this is to set the fuel pump timing correctly. Additionally, if there is a dirty fuel filter then it should be cleaned out as part of the maintenance process. Finally, if the engine has not been fully warmed up before use then this could also cause stalling so make sure to warm up the engine first.
- Engine stalls after starting: The engine was stalling after starting due to a dirty fuel filter. To remedy this, the technician replaced the filter element and inspected the fuel injection pump for proper operation. If needed, they could rebuild or install a new injection pump. Additionally, it was found that the air filter element had become clogged and so it too had to be replaced in order to keep the vehicle operating properly.
- Engine is overheated: The engine is overheated due to several factors. Firstly, the radiator core may be clogged or the radiator cap may be leaking; both of these can easily be remedied by either cleaning the radiator or replacing the cap. Low engine coolant may also cause an overheat; if this is found to be true, it should be refilled to its correct level and checked for any possible leaks in the system. Additionally, a loose or defective fan belt could also contribute to an overheat; belt replacement is recommended in order to rectify this issue. Lastly, lack of engine oil can lead to an overheat as well; it must then simply be added back into the engine crankcase in order for everything to run smoothly again.
- Loss of engine power: When experiencing a loss of engine power, one should check the injection nozzles for dirt or damage and replace them if necessary. Additionally, it is important to service fuel hoses and lines in case they are blocked. Restricted intake air can be solved by replacing the air filter element. Finally, worn cylinder head gasket could be causing the problem; in this case it needs to be replaced with a new one.
- Engine noises or knocks: When diagnosing engine noises or knocks, it is important to assess the coolant temperature and ensure that it is up to the required level. Additionally, if the engine oil level is low, it must be filled back up. Furthermore, a potential cause for these issues can be an incorrect setting of fuel injection pump timing; this must be set correctly as recommended. If there are worn or broken pistons present, they should be replaced immediately. Finally, if misalignment or defectiveness in the connecting rod is suspected then action needs to be taken to change and/or align it as necessary.
- Engine stalls while idle: When an engine stalls while idle, this is usually due to incorrect adjustment of low idle speed or incorrect valve clearance. To rectify this issue, it is necessary to adjust the low idling as recommended and correct any discrepancies in the valve clearance. In some cases, such as with fuel injection pump malfunction, a replacement or rebuild of the injection pump may be necessary.
- Oil pressure is insufficient: Oil pressure is insufficient, indicating that the oil level is low. To remedy this, additional oil should be added as necessary. If the issue persists, it may be indicative of a worn or damaged oil pump; in such an instance, repair or replacement would need to occur. In addition, if the engine oil filter element has become clogged with debris and dirt, then replacing or servicing it could also help alleviate the issue with insufficient oil pressure.
2.Transmission Troubleshooting

- Transmission is making noise: Transmission noise can be caused by a variety of problems, including damaged or incorrectly adjusted gears, worn or bent shift forks, worn shaft splines, lack of transmission oil supply, and worn or broken bearings. If the gears are damaged or the backlash is incorrect they must be replaced. Similarly if the shift forks are too worn then they should be changed as well. Additionally if the shaft splines are worn then a new shaft needs to be installed. To address any lack of transmission oil supply it is important to check and add oil as necessary. Finally for any issues with bearing replacements these should also be done in order to resolve any issues causing unwanted noise from the transmission system. Furthermore if there is contamination in the transmission oil this should also be changed immediately in order to ensure optimal performance from this vital component of your vehicle’s drivetrain system.
- Difficult to shift gears: When faced with difficulty shifting gears, the cause may be due to a worn or rusty gear shift linkage. To address this issue, a new shift linkage should be installed. Additionally, an unadjusted or worn clutch may need to be adjusted or replaced as necessary. If there are any worn or bent shift forks present, they will need to be replaced as well. Lastly, if the gear shifting mechanism is found to have been worn from use over time, the appropriate components must either be repaired or changed out for new ones in order for it to function correctly again.
- Low transmission oil pressure: Low transmission oil pressure is an issue that can occur due to a lack of transmission oil supply. It is important to regularly check the transmission oil level and add any necessary additional oil as required. Additionally, if there is a dirty transmission filter element equipped, it should be serviced or replaced. If there appears to be a defective relief valve present, it should also be replaced for optimal functioning of the transmission system.
- Transmission fluid leaks: Transmission fluid leaks can be caused by damaged gaskets or seals, in which case they need to be replaced. If the transmission oil level is too high, it needs to be corrected to the correct volume in order for the leak to stop. It is important that any repairs are done professionally and promptly, as a transmission fluid leak can lead to further damage if left unchecked.
3.Hydraulic System Troubleshooting
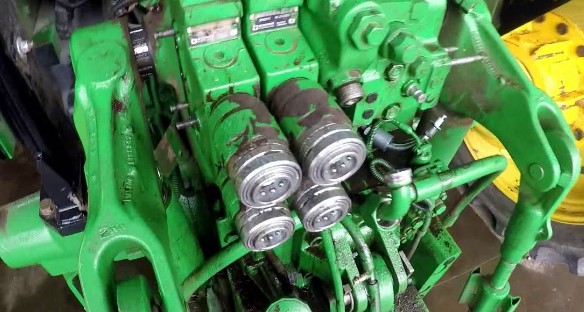
- Hydraulics overheating: Hydraulic overheating is a common problem that can occur when the hydraulic oil type is incorrect, or if there is contamination of the oil. To resolve this issue, the correct type of oil must be poured into the system. Additionally, if there is air in the hydraulic system, it must be bled out to ensure proper functionality. Lastly, if there are any issues with main relief valve malfunction, then it should be replaced immediately as part of a preventative maintenance plan.
- Hydraulic fluid pressure is low: Hydraulic fluid pressure being low is a sign that there may be an underlying problem with the system. It may be due to insufficient hydraulic oil, a dirty filter element, leaks in the lines, control valve setting errors or pump malfunctions. The necessary actions must be taken to address these issues promptly. To ensure proper operation of the hydraulic system, it is important to check and refill the hydraulic oil as needed; replace or service the filter element if required; repair any leaks detected; adjust the control valves correctly; change or repair any malfunctioning pumps and cylinders respectively.
- Hitch can’t lift or lifts too slowly: The hitch is unable to lift, or lifts too slowly due to a defective hydraulic pump. In order to remedy this situation, it will be necessary to change or repair the hydraulic oil pump, install a new main relief valve if the current one is damaged, repair or replace the faulty hydraulic control valve and cylinder, check the level of hydraulic oil and add more if needed, and switch out any clogged filter elements or service them as required. If there appears to be an excessive load on the hitch then steps should also be taken in order to reduce that load accordingly.
- Three-point hitch cannot be dropped or dropping is too slow: The three-point hitch cannot be dropped or is dropping too slow due to hydraulic cylinder failure. To remedy this, the hydraulic cylinder must be repaired or replaced. Additionally, it may also be caused by an incorrect setting of the hydraulic control valve; therefore, adjusting it to the correct setting can fix the issue as well. If these two solutions do not work, then worn lift arm shaft could be the problem and must then be changed. Finally, if all other issues have been checked for and no solution has been found yet, then adjustments need to made on the three-point hitch itself.
- 3-point hitch jerks when lower or lift: The 3-point hitch of a tractor may jerk when it is lifted or lowered, which could be caused by hydraulic fluid contamination. To fix this issue, new hydraulic fluid should be filled up in the system. A potential cause for the problem could also be attributed to a failed hydraulic pump, so replacing or repairing it can address the situation. Additionally, air in the hydraulic pipes can cause jerks and therefore needs to be bled out from them. Lastly, if there is an issue with the defective spool valve then that needs to either need to repaired or replaced with a newly installed one. If none of these solutions work then it might suggest that there is something wrong with the broken cylinder which requires repair or replacement as well.
See also: Mahindra Tractor Warning Lights Meaning
4.Steering Troubleshooting
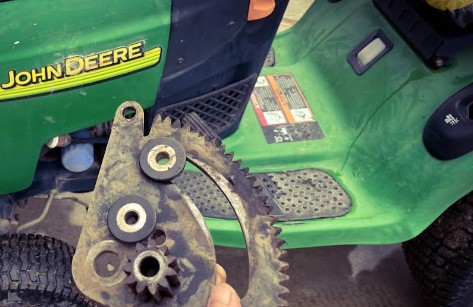
- Steering wheel free play is excessive: Steering wheel free play is excessive due to maximum wear on the steering column shaft or coupling. A defective part needs to be replaced, and if there is damage to the hydraulic steering pump it must be replaced or repaired. Additionally, loose or worn out steering linkage components should be inspected and repaired as necessary. Lastly, it may also be necessary to inspect and replace the power steering control valve if there is any damage or wear present.
- Steering wheel is hard to turn: The steering wheel may be hard to turn if air is trapped inside the system, in which case it must be bled. Additionally, a dirty steering filter element needs cleaning or replacing, and insufficient steering oil requires adding more to the system. The power steering control valve may need inspecting and replacing if there are malfunctions or wear present. If the hydraulic steering pump is not working correctly, it should be checked and changed as necessary. The pump flow control valve may also need changing or flushing if it is damaged or stuck. Lastly, a damaged or incorrectly assembled steering column should either be replaced or re-assembled properly; uneven front tire wear could necessitate new tires being fitted instead; not adjusting toe-in would require checking for correct alignment; and any leaking of the steering cylinder will mean replacing worn seal sleeves or repairing a damaged piston rod.
- Front wheels wander to right or left: Front wheels may wander to the right or left, which can indicate damage or wear on the power steering control valve. An inspection and potential replacement should be done as required. This issue may also be due to a damaged steering cylinder, requiring either repair or replacement of the hydraulic steering cylinder. Incorrect toe-in can cause this issue as well; therefore, it is important to adjust toe-in wheels if necessary. Steering linkage joints that are worn or loose will require repair or replace of the steering linkage itself, while front wheel bearings that are damaged or incorrectly adjusted need to be changed/adjusted properly in order for them to function correctly. Finally, uneven front tyre wear could likely necessitate changing out both tyres for new ones.
See also: Jlg Boom Lift Warning Lights
5.Electrical System Troubleshooting
- Battery does not charge: If a battery does not charge, the electrical connections may be corroded or loose. To remedy this issue, these connections must be cleaned and tightened, if possible. If the terminal connectors are defective then they will need to be changed out for new ones. It is also possible that the battery itself has a dead cell which would require it to be replaced entirely. Lastly, if the belt is worn or loose then tension needs to be adjusted or a replacement belt should be installed instead.
- Starter motor cranks slow: A starter motor cranking slowly is often a sign of low battery output. Low charging and draining quickly can be signs that the battery needs to be serviced or replaced. Faulty connections or disconnected cables may also cause this issue, so it’s important to check and ensure proper wiring is connected or new terminals are installed if necessary.
- Starter motor is not working: The starter motor is not working, likely due to a discharged or worn battery. To fix this issue, the battery must either be recharged or replaced. Additionally, the wiring harness may have become disconnected or improperly connected. It should be checked and reconnected as necessary. If the battery capacity is low, charging it will resolve that issue as well. Lastly, if all of these solutions do not work then there might be damage to the starter motor itself which would require repairing it or replacing it altogether.
See also: John Deere Gator 825i Warning Lights
This article has provided a comprehensive overview of the common problems that novice users may encounter when utilizing the John Deere 3025d model. It also offers solutions to these issues, making it an invaluable resource for those navigating this extraordinary piece of machinery. Ultimately, this article is an asset to anyone seeking guidance on how best to use and troubleshoot the John Deere product.
I own a John Deere 3025d and know the struggles of dealing with these problems first hand. I recently had an issue with the wiring and had to take it to a mechanic. It ended up being a faulty connection and the mechanic was able to fix it quickly.
If you experience any electrical problems with the John Deere 3025d, it’s best to take it to a professional as soon as possible. If it’s caught early, it will save you a lot of time and money in the end.
Has anyone else had any issues with their John Deere 3025d? What did you do to fix the problem? I’d love to hear your stories and experiences dealing with this tractor.